Jig/Fixture design is generally carried out in accordance with the specific requirements of a certain process after the formulation of the machining process of parts. The possibility of fixture realization should be fully considered in the formulation of process. When designing jig, if necessary, modification suggestions can be put forward for the process.
The Jig design quality should be measured as per following standard:
- the machining quality of workpiece can be stably guaranteed
- the production efficiency is high
- the cost is low
- the chip removal is convenient
- the operation is safe
- labor-saving
- the manufacturing and maintenance are easy
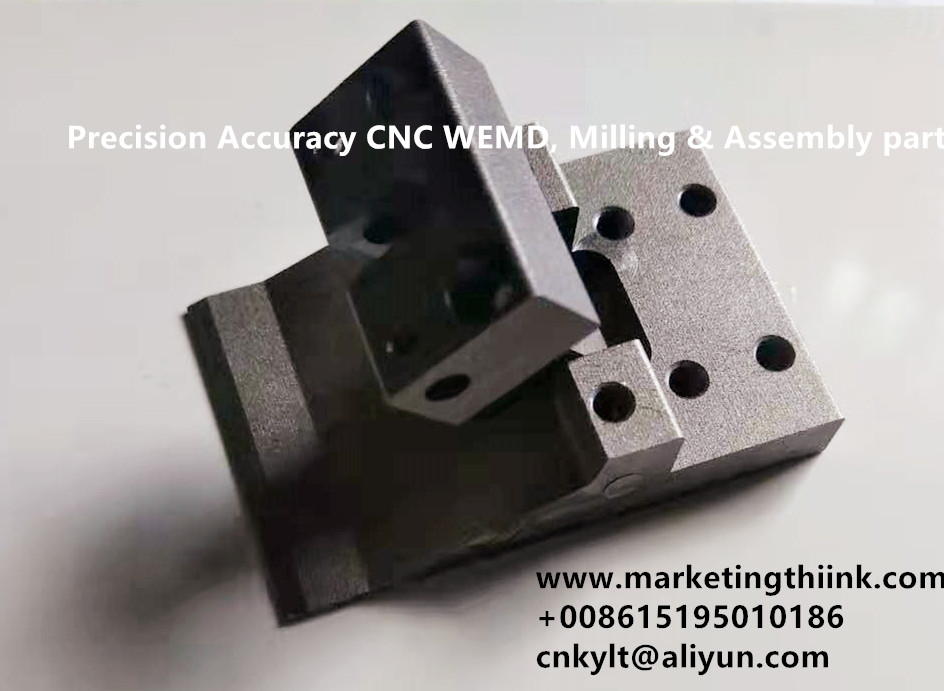
Basic Principles of Jig design
- Meet the stability and reliability of workpiece positioning during use;
- There is enough bearing or clamping force to ensure the processing process of workpiece on tooling fixture;
- Meet the requirements of simple and fast operation in the clamping process;
- Vulnerable parts must be of a structure that can be replaced quickly, and it is better not to use other tools when conditions are sufficient;
- Meet the reliability of repeated positioning of fixture during adjustment or replacement;
- Try to avoid complicated structure and high cost;
- Select standard parts as component parts as much as possible;
- Form the systematization and standardization of the company’s internal products.
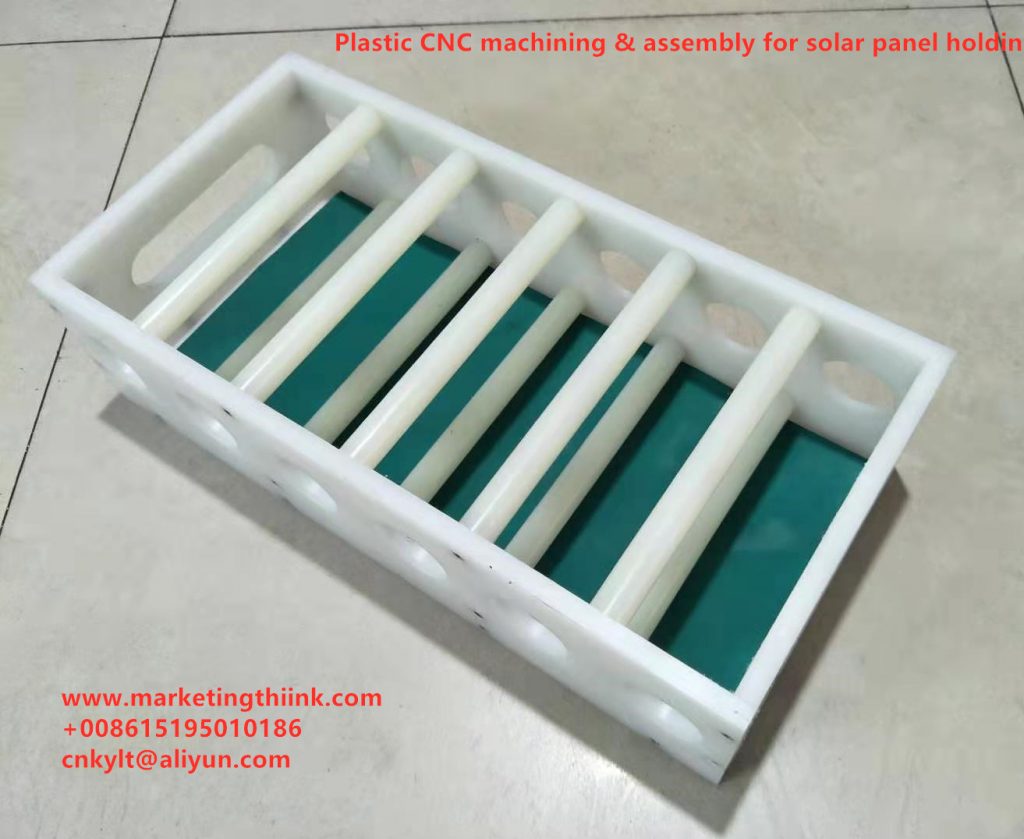
Basic knowledge of Jig design
A GOOD JIG MUST MEET THE FOLLOWING BASIC REQUIREMENTS:
- The key to ensure the machining accuracy of workpiece lies in the correct selection of positioning datum, positioning method and positioning elements, and the analysis of positioning error if necessary. Attention should be paid to the influence of the structure of other parts in the fixture on the machining accuracy to ensure that the fixture can meet the machining accuracy requirements of workpiece.
- The complexity of the special fixture for improving production efficiency should be adapted to the production capacity. Various fast and efficient clamping mechanisms should be adopted as far as possible to ensure convenient operation, shorten the auxiliary time and improve production efficiency.
- The structure of special fixture with good process performance shall be simple and reasonable to facilitate manufacturing, assembly, adjustment, inspection, maintenance, etc.
- The fixture with good performance shall have sufficient strength and rigidity, and the operation shall be simple, labor-saving, safe and reliable.
- On the premise that the objective conditions permit and are economical and applicable, pneumatic, hydraulic and other mechanical clamping devices should be used as far as possible to reduce the labor intensity of the operator. The fixture shall also be convenient for chip removal. If necessary, the chip removal structure can be set to prevent the chip from damaging the positioning of the workpiece and damaging the tool, so as to prevent the chip from accumulating and bringing a lot of heat to cause the deformation of the process system.
- Special clamps with good economy shall adopt standard components and structures as much as possible, and strive to be simple in structure and easy to manufacture, so as to reduce the manufacturing cost of clamps. Therefore, in order to improve the economic benefit of fixture in production, the necessary technical and economic analysis should be carried out according to the order and production capacity.
KYLT Precision CNC machining services (milling & turning service), Fast prototyping, Fixture/Jig/Tooling making, Aluminum die casting & plastic injection parts. Email:cnkylt@aliyun.com +008615195010186
KYLT CNC Machining Services:
KYLT CNC Precision Machined Parts:
More information about Machining Technology:
评论
发表评论