Zinc die casting (Zamak alloy injection) is highly popular for making parts in Metal decoration, building and industrial fields. KYLT provide precison Zinc/Zamak injection and Aluminum die casting servcie.
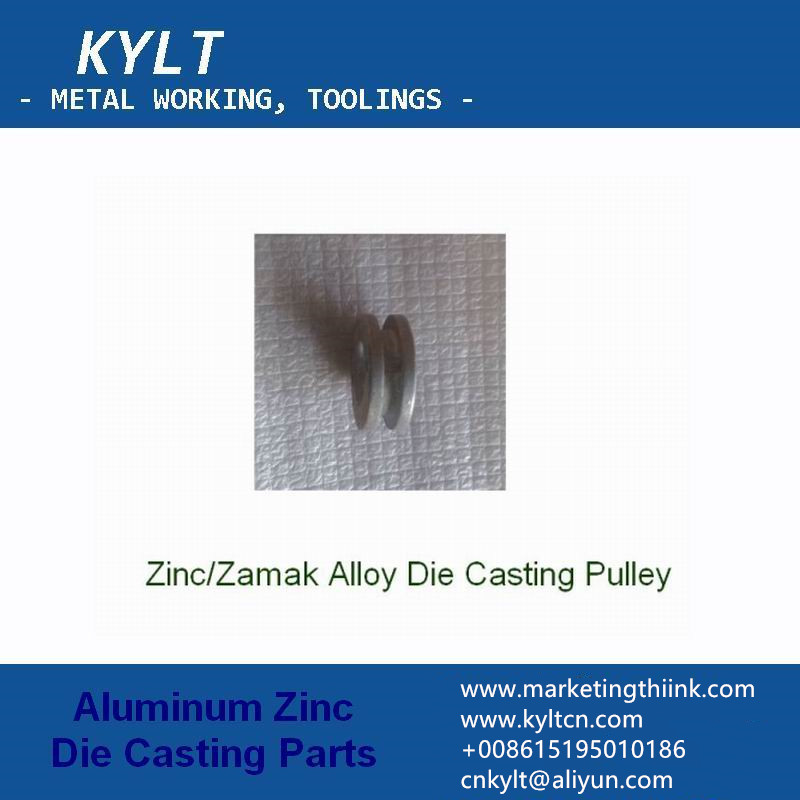
Which machines used to inject Zinc alloy?
Cold chamber die casting machine: this machine used to make big size and heavy zinc alloy part.
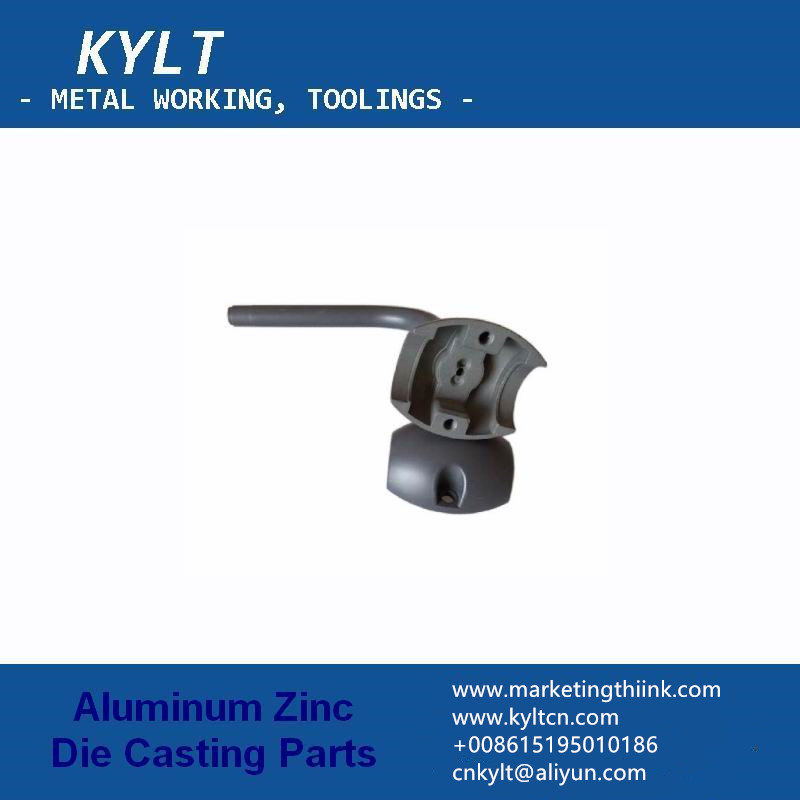
Hot chamber die casting machine: this type is used to cast small size zinc part.
HOT CHAMBER DIE CASTING MACHINE CAN BE CLASSIFIED :
vertical zinc injection machine: which used to cast bick, car, motor cycle brake wire with zinc end.
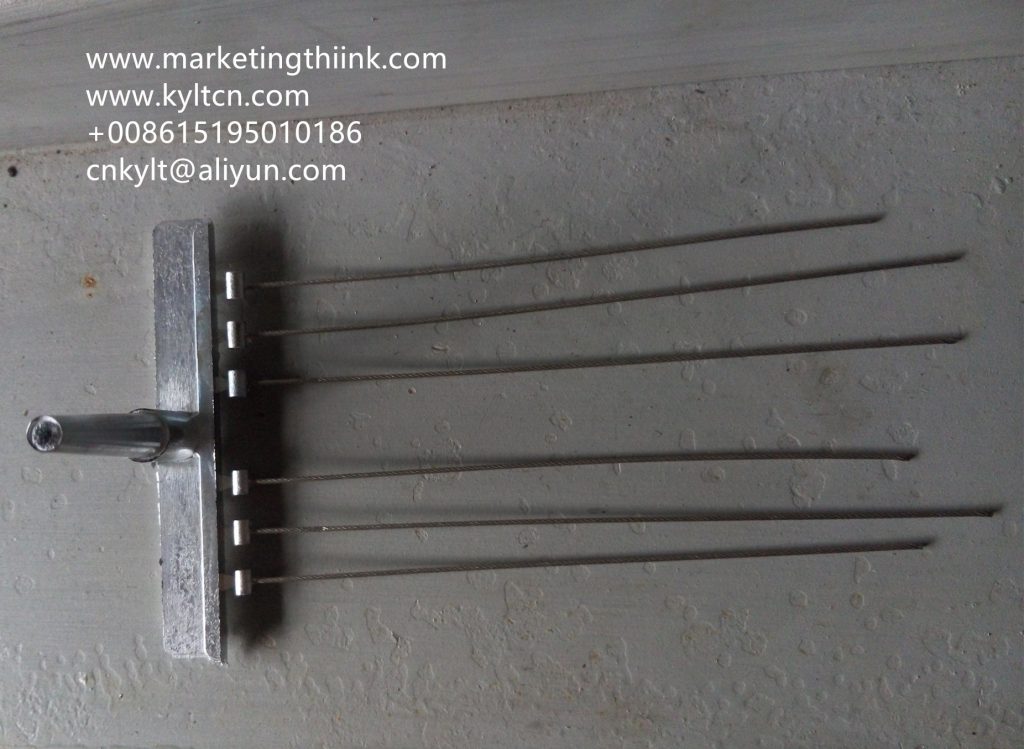
horizontal zinc injection machine: which used to inject zipper, electrical spare part, jewelry etc.
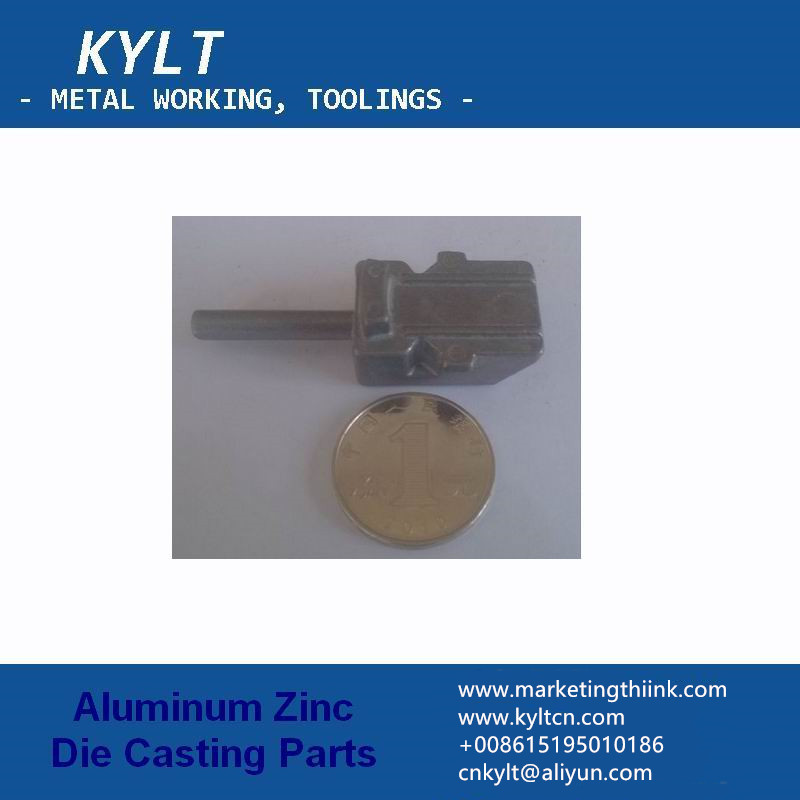
With casting process there is often no need of further machining after casting: not only its accuracy is up to 99.8%, but casted products also can be used raw, since they have a pleasant finish. Zinc die casting usage is almost 28% in automotive industry, followed by building and hardware sectors.
Moreover, zinc can be the right choice to obtain high quality aesthetic components, with strict tolerances impossible to achieve with other materials, and to obtain embossing and grooves for mechanical or gear components.
By using zinc and its alloys is possible to produce components capable of reaching high aesthetic quality , with strict and narrow tolerances for shapes morphology. Zinc alloy is also used for plating purposes because of its many benefits, such as enhancing the already impressive anti-corrosion zinc properties.
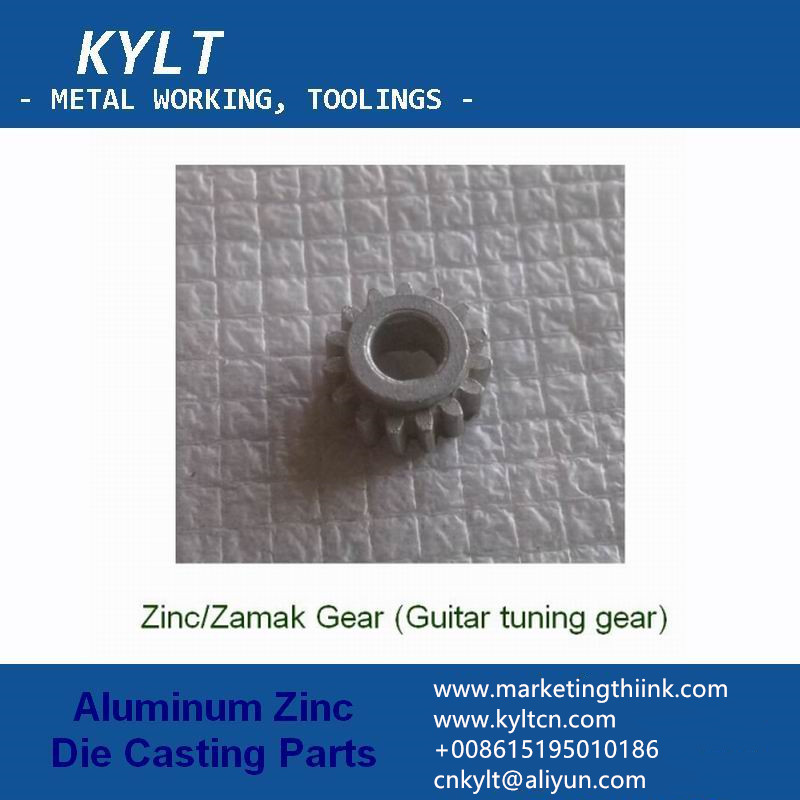
What are the advantages of Zinc alloy?
Zinc alloys in die casting allows to develop products and to simplify production, providing a durable end-product. Zinc strength, ductility and stability allows specialists to obtain a better and more resistant product. It is this high ductility that makes zinc ideal for die casting process, in which it is necessary to sustain pressure and expansion without fracturing. Other zinc alloys advantages are used in die casting, such as:
- Electrical and thermal conductivity
- Raw material low cost
- Strong stability, which grants a long-lasting end product with high quality finishing properties
- Thin walls: they contribute to corrosion resistance for end products, increasing their durability in harsh environment
- Economical for small parts
- Low melting point, which means it requires less energy for production
- Dies have a longer tool life
- Complex geometries and quality finishing: by using zinc it is possible to cast intricate, thin walled and technically demanding parts with high precision
- Top quality coating and chrome plating: zinc die casting components are fit for electroplating
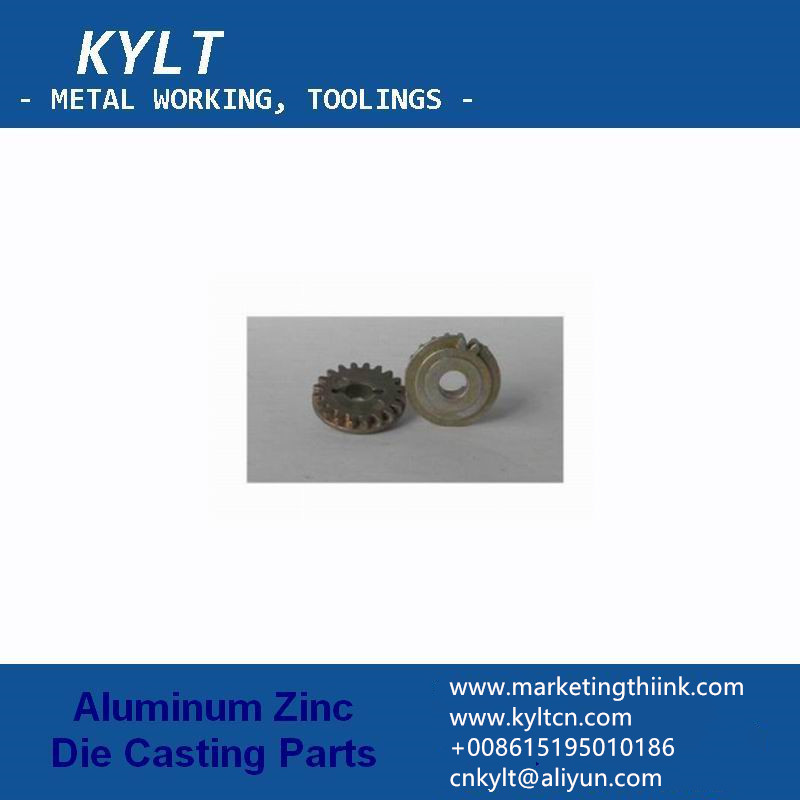
KYLT Precision CNC machining services (milling & turning service), Fast prototyping, Fixture/Jig/Tooling making, Aluminum die casting & plastic injection parts. Email:cnkylt@aliyun.com +008615195010186
KYLT CNC Machining Services:
KYLT CNC Precision Machined Parts:
More information about Machining Technology:
评论
发表评论