Introduction
Plastic injection molded parts have become indispensable in various industries, thanks to their versatility, cost-effectiveness, and ease of production. However, there has always been a demand for enhancing the appearance and functionality of these parts. Enter UV Vacuum Metallization Coatings – a revolutionary technology that has taken plastic injection molding to new heights. In this article, we will delve into the world of plastic injection molded parts with UV Vacuum Metallization Coatings and explore how they are transforming the manufacturing industry.
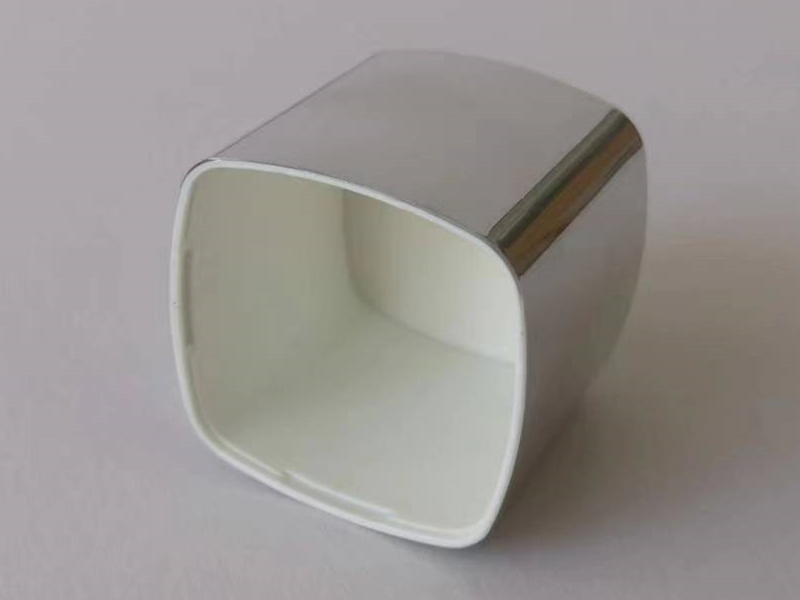
(Plastic cosmetic packaging parts making and UV vacuum metallization coating service: cnkylt@aliyun.com)
1. Understanding Plastic Injection Molded Parts with UV Vacuum Metallization Coatings
Plastic injection molded parts with UV Vacuum Metallization Coatings refer to plastic components that undergo a specialized process where a thin layer of metallic coating is applied to their surface using vacuum deposition techniques. This process involves evaporating a metal, such as aluminum, in a vacuum chamber, and allowing the metal vapor to condense on the plastic surface, resulting in a uniform, reflective coating.
2. Benefits of UV Vacuum Metallization Coatings for Plastic Injection Molded Parts
Plastic injection molded parts with UV Vacuum Metallization Coatings offer many benefits that make them a game-changer in the manufacturing industry. Let’s explore some of these advantages:
2.1. ENHANCED AESTHETIC APPEAL
With UV Vacuum Metallization Coatings, plastic parts can achieve a high-end metallic appearance that mimics the look of chrome, stainless steel, or other desired finishes. This opens up new possibilities for designers and manufacturers to create visually appealing products that stand out in the market.
2.2. IMPROVED DURABILITY
The metal layer provided by UV Vacuum Metallization Coatings adds a protective barrier to plastic parts, making them more resistant to wear, scratches, and corrosion. This significantly extends the lifespan of the components and enhances their overall durability.
2.3. INCREASED REFLECTION AND SHINE
The reflective nature of the metallic coating enhances the part’s shine and creates an attractive mirror-like effect. This feature is particularly valuable in applications where aesthetics and visual impact play a crucial role, such as automotive interiors, consumer electronics, and decorative items.
2.4. VERSATILE APPLICATIONS
Plastic injection molded parts with UV Vacuum Metallization Coatings find applications in numerous industries, including automotive, electronics, cosmetics, and household goods. They are used in various products, such as interior trim components, cosmetic packaging, consumer electronics casings, and more.
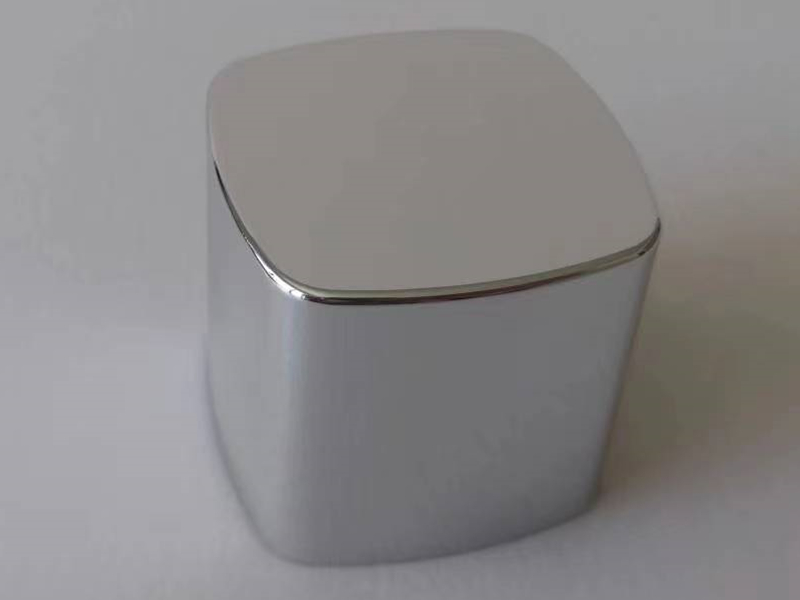
(Plastic cosmetic packaging parts making and UV vacuum metallization coating service: cnkylt@aliyun.com)
3. The UV Vacuum Metallization Process for Plastic Injection Molded Parts
To achieve the UV Vacuum Metallization Coatings on Plastic injection molded parts, a multi-step process is followed. Let’s take a closer look at each of these steps:
3.1. SURFACE PREPARATION
Before the metallization process, the plastic parts undergo thorough cleaning and surface preparation. This involves removing any contaminants, oils, or residues that could affect the adhesion of the metallic coating. The surface is typically cleaned using chemical treatments and plasma etching.
3.2. BASECOAT APPLICATION
After the surface preparation, a basecoat is applied to the plastic part. The basecoat acts as a bonding layer between the plastic substrate and the metallic coating. It ensures good adhesion and enhances the overall durability and performance of the metallized part.
3.3. VACUUM METALLIZATION
Once the basecoat is applied, the plastic parts are loaded into a vacuum chamber. Inside
the chamber, a high vacuum is created, and the metal, typically aluminum, is heated until it evaporates. The metal vapor then condenses onto the surface of the plastic parts, creating a thin and uniform metallic layer. This process, known as vacuum deposition, ensures precise and consistent coating thickness across all the parts.
3.4. UV CURING AND TOPCOAT APPLICATION
After the vacuum metallization step, the coated plastic parts undergo UV curing. This involves exposing the parts to ultraviolet light, which helps in curing and hardening the base coat and the metallic layer. Once the UV curing is complete, a protective topcoat is applied to provide additional durability, scratch resistance, and UV resistance to the metalized parts.
3.5. QUALITY CONTROL AND INSPECTION
To ensure the highest quality standards, the metalized parts undergo rigorous quality control and inspection processes. This includes visual inspection, measurement of coating thickness, adhesion testing, and performance evaluation. Any defective parts are identified and corrected to maintain the desired quality level.
(Plastic cosmetic packaging parts making and UV vacuum metallization coating service: cnkylt@aliyun.com)
4. Applications of Plastic Injection Molded Parts with UV Vacuum Metallization Coatings
Plastic injection molded parts with UV Vacuum Metallization Coatings find extensive applications across various industries. Let’s explore some of the key areas where this technology is making a significant impact:
4.1. AUTOMOTIVE INDUSTRY
The automotive industry utilizes plastic injection molded parts with UV Vacuum Metallization Coatings for interior trim components, such as center console panels, dashboard trims, door handles, and gearshift knobs. The metallic finishes add a touch of luxury and elegance to the car interiors, enhancing the overall aesthetic appeal.
4.2. CONSUMER ELECTRONICS
In the consumer electronics sector, UV Vacuum Metallization Coatings are applied to plastic parts of devices like smartphones, laptops, gaming consoles, and audio equipment. The metallic coatings not only enhance the visual appeal but also provide added protection and durability to the components.
4.3. COSMETICS AND PACKAGING
Plastic packaging plays a crucial role in the cosmetics industry, and the use of UV Vacuum Metallization Coatings adds a premium and eye-catching appearance to cosmetic containers, perfume bottles, and compact cases. The reflective and shiny finishes create a sense of sophistication and luxury, attracting consumers’ attention on store shelves.
4.4. HOUSEHOLD GOODS AND DECORATIVE ITEMS
From home appliances to decorative items, UV Vacuum Metallization Coatings are widely utilized in various household goods. Plastic parts of items like kitchen appliances, bathroom fixtures, lighting fixtures, and decorative trims can be metallized, elevating their visual appeal and making them stand out in the market.
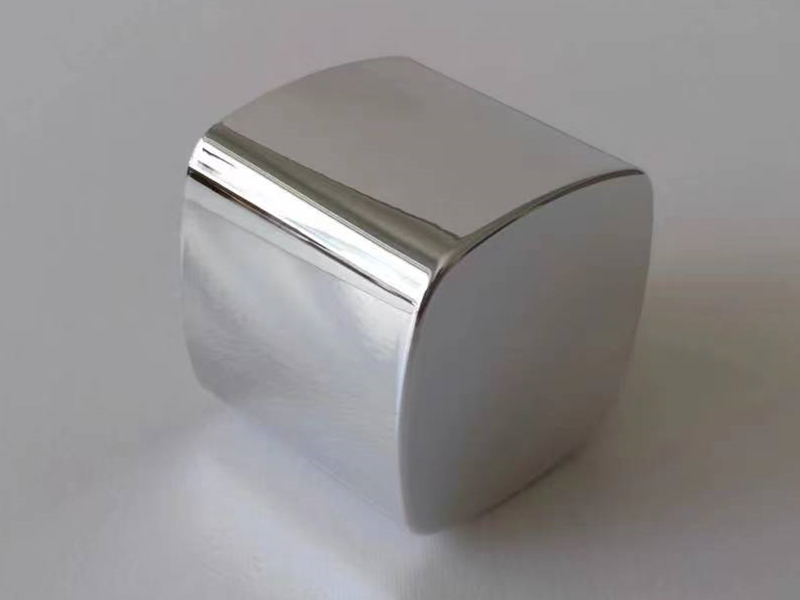
(Plastic cosmetic packaging parts making and UV vacuum metallization coating service: cnkylt@aliyun.com)
5. Frequently Asked Questions (FAQs)
Here are some frequently asked questions about plastic injection molded parts with UV Vacuum Metallization Coatings:
5.1. CAN ANY TYPE OF PLASTIC BE METALIZED USING UV VACUUM METALLIZATION COATINGS?
Yes, UV Vacuum Metallization Coatings can be applied to a wide range of plastic materials, including ABS, PC/ABS, PC, PMMA, and more.
5.2. WHAT ARE THE MAIN ADVANTAGES OF USING UV VACUUM METALLIZATION COATINGS COMPARED TO TRADITIONAL PAINTING OR PLATING PROCESSES?
UV Vacuum Metallization Coatings offer superior adhesion, enhanced durability, improved scratch resistance, and a high-quality metallic appearance that cannot be achieved with traditional painting or plating processes.
5.3. ARE THE METALIZED PLASTIC PARTS ENVIRONMENTALLY FRIENDLY?
Yes, the metallized plastic parts are environmentally friendly. The process of vacuum deposition does not involve the use of harmful chemicals or generate significant waste. Additionally, the durability of the coatings contributes to the longevity
of the plastic parts, reducing the need for frequent replacements and minimizing environmental impact.
5.4. CAN UV VACUUM METALLIZATION COATINGS BE CUSTOMIZED TO ACHIEVE DIFFERENT FINISHES?
Yes, UV Vacuum Metallization Coatings offer versatility in terms of finishes. By selecting different metals and adjusting the deposition parameters, various finishes such as chrome, gold, copper, and even unique patterns can be achieved, allowing for customization to meet specific design requirements.
5.5. HOW LONG DOES THE UV VACUUM METALLIZATION COATING LAST?
The durability of UV Vacuum Metallization Coatings depends on factors such as the quality of the coating, the application, and the level of exposure to environmental conditions. However, when applied correctly, these coatings can provide long-lasting performance and maintain their appearance for extended periods.
5.6. CAN METALLIZED PLASTIC PARTS BE RECYCLED?
Metalized plastic parts can be recycled, but the recycling process involves separating the plastic from the metallic coating. Specialized recycling techniques are required to recover the valuable metal and recycle the plastic separately.
(Plastic cosmetic packaging parts making and UV vacuum metallization coating service: cnkylt@aliyun.com)
6. Conclusion
Plastic injection molded parts with UV Vacuum Metallization Coatings have revolutionized the manufacturing industry, offering enhanced aesthetics, improved durability, and versatile applications. With their ability to create high-quality metallic finishes, these parts have found their place in automotive interiors, consumer electronics, cosmetics, and household goods. The UV Vacuum Metallization process, coupled with advanced surface preparation and quality control, ensures the production of durable, visually appealing, and environmentally friendly components.
As technology continues to advance, UV Vacuum Metallization Coatings hold immense potential for further innovations and applications. From automotive advancements to cutting-edge electronics, the utilization of metalized plastic parts will continue to shape the future of manufacturing.
KYLT provides a “ONE-STOP SERVICE” of Plastic cosmetic packaging parts injection molding and UV vacuum metallization coating. To get A FREE quotation for your UV-coated ABS, PC, PP material cosmetic package parts price, please Email us: cnkylt@aliyun.com
KYLT CNC Machining Services:
Home>CNC Machining Services>CNC Milling Services
Home>CNC Machining Services>CNC Turning Services
Home>CNC Machining Services>Rapid Prototyping Services
Home>CNC Machining Services>Injection Molding Services
KYLT CNC Precision Machined Parts:
Home>Precision CNC Machined Parts
Home>Precision CNC Machined Parts>CNC Precise Turned Parts
Home>Precision CNC Machined Parts>CNC Precise Milled Parts
Home>Precision CNC Machined Parts>Aluminum Machining
Home>Precision CNC Machined Parts>Magnesium Machining
Home>Precision CNC Machined Parts>Copper & Brass Machining
Home>Precision CNC Machined Parts>Steel Machining
Home>Precision CNC Machined Parts>Stainless Steel Machining
Home>Precision CNC Machined Parts>Plastic Machining
More information about Machining Technology:
评论
发表评论